Exploring high-entropy alloys
Kathryn Anne Quelle
Nov 6, 2018
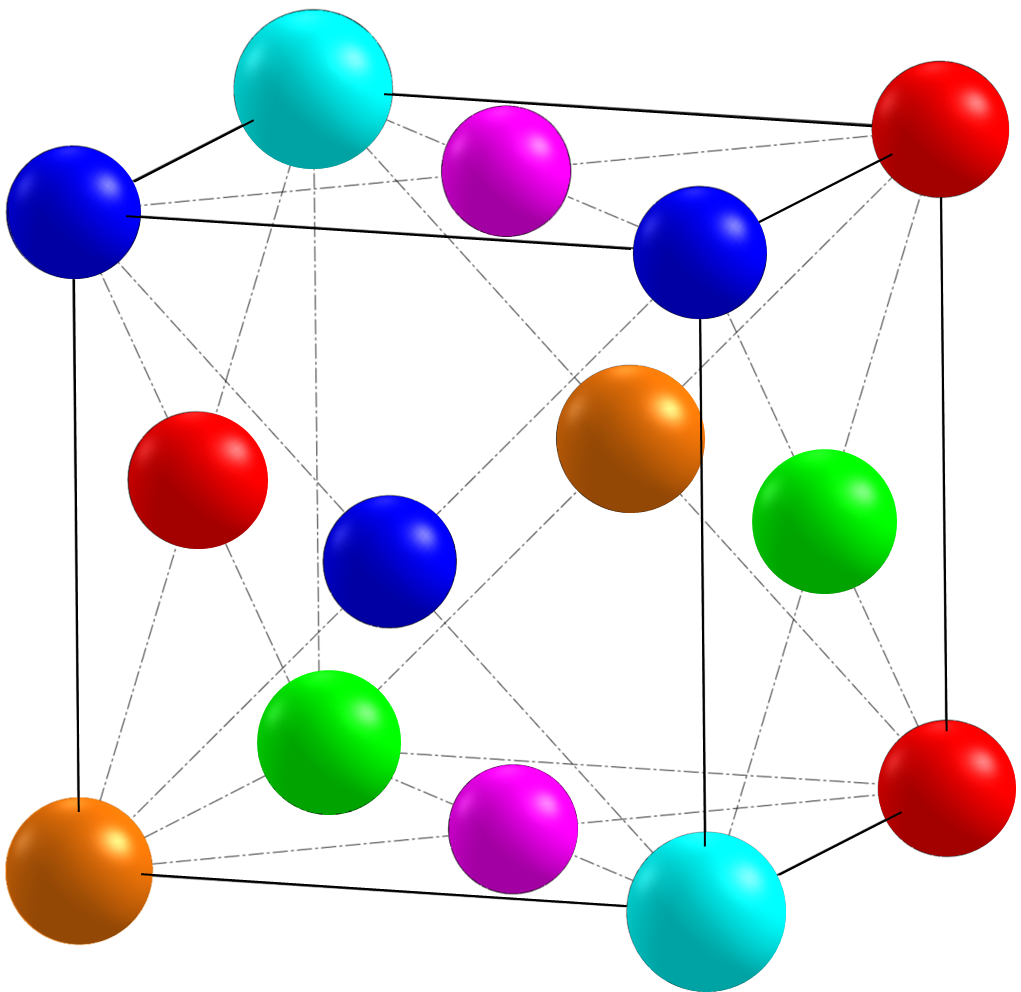
Source: Carnegie Mellon University
A high-entropy alloy is a solid solution in which different atoms are randomly located at lattice sites, yet still form a crystalline structure.
Carnegie Mellon Mechanical Engineering Professor Maarten de Boer, Machine Learning Associate Professor Barnabas Poczos, and Materials Science and Engineering Assistant Professor Bryan Webler received a Manufacturing Futures Initiative (MFI) award for their new collaborative project with high-entropy alloys, a new class of metal alloy. All three researchers are also affiliated with CMU’s additive manufacturing research center, the Next Manufacturing Center, and will synthesize their high-entropy alloy laboratory specimens using additive manufacturing methods.
Traditional alloys are made up of one base metal – typically more than 50 percent by mass – and small concentrations of additional alloying elements. Alternatively, high-entropy alloys are composed of metals all in roughly equal concentrations. These alloys were originally named for their high configurational entropy due to the number of different ways their elements can combine.
Pure metals rarely perform acceptably in engineering applications, but alloying can introduce a wide variety of properties and open up possibilities. Special metal alloys, known as superalloys, are commonly used in aerospace power generation applications, which means that these metals have to perform well at very high temperatures. However, even superalloy performance decreases as it heats up, which threatens structural integrity. A high-entropy alloy can have interesting strength, magnetic, and electrical properties. De Boer, Poczos, and Webler intend to “investigate if there’s a way to get good performance at higher temperatures with this new class of metals.”
In particular, Webler says the group will focus on resistance to chemical reactions, such as oxidation. Every metal except gold wants to react with oxygen above room temperature, but some metals are more resistant than others. Because previous research has suggested that high-entropy alloys may perform better than traditional alloys at high temperatures in reactive environments, the three researches plan to explore how these alloys react at high temperatures. De Boer says, “If we can make these alloys oxidize more slowly at higher temperatures, that would have a huge impact.”
Unfortunately, high-entropy alloys are complex and expensive to produce, and it would be unreasonable to try and make a structure purely out of these alloys. Instead, de Boer, Poczos, and Webler plan to coat structures with high-entropy alloys. Ideally, these coatings will be stronger and more stable than the underlying metals, making overall structures last longer without costing too much.
So far, researchers have studied high-entropy alloys’ properties by working with them in the form of small buttons that they produce at the laboratory scale using conventional melting and casting processes. The three researchers will design and synthesize their specimens using powder-based additive manufacturing methods, which can later be applied to coating large structural components. However, because synthesizing the alloys is expensive, a large part of their research will rely on machine learning. Poczos will contribute his machine learning expertise so that they can predict alloy properties and modify conditions quickly and accurately.
Using machine learning, de Boer, Poczos, and Webler can design high-entropy alloys more easily and run simulations before moving on to lab testing.
High-entropy alloy research could have immense impacts, such as making engines more efficient and effective by allowing them to run at higher temperatures. De Boer, Poczos, and Webler are still unsure where exactly their research will take them because, as Webler says, “You’re thinking about the entire periodic table and just picking elements and mixing them together so there are many possible combinations.”
Carnegie Mellon’s Manufacturing Futures Initiative (MFI) awards fund multidisciplinary, collaborative projects of two or more faculty members. MFI awards specifically support research incorporating machine intelligence into manufacturing environments.
Media contacts:
Lisa Kulick, College of Engineering
lkulick@andrew.cmu.edu
Byron Spice, School of Computer Science
bspice@cs.cmu.edu